The article “Design for Manufacture and Assembly” describes the process of analyzing product design in order to identify design changes that will improve assembly and manufacturing. In this article writer describes the importance of Design for Manufacture and Assembly in cost reduction, and product quality benefits and has presented the case study regarding the application of Design for Manufacture and Assembly in gunsight mechanism.
Introduction
After the 1980s the process of product development completely changed. According to the writer redefinition of the expected outcome of the activity of design for manufacture and establishment of new procedures for product development in which product performance and the required manufacturing procedures for the product are considered together from the earliest concept stages of a new design are the major two seeds that have been followed since then and was adopted in the development of consumer products where the title of simultaneous engineering or concurrent engineering was usually given to it.
The simultaneous engineering term was introduced in the 1980s. Establishing the cross-functional product development team is the main element in simultaneous engineering. Simultaneous engineering is about addressing two main things first is meeting the customer performance requirement and second is cost and quality goals. Due to this reason, simultaneous engineering is the accepted method of product development. So, in this paper, the writer has presented his ideas of design for manufacture and assembly in order to give the customer demand products with quality and manufacture and assembly feasibility for companies.
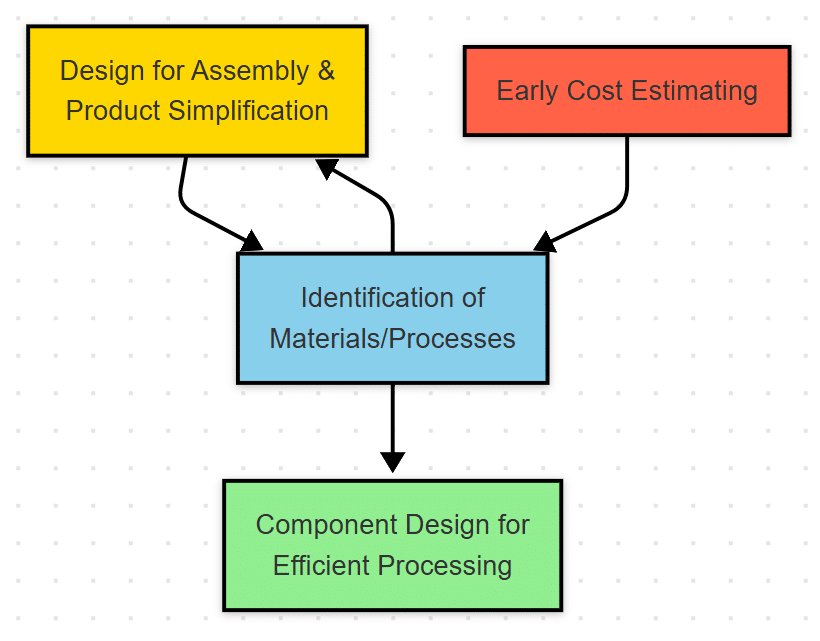
The purpose of this article is to find out the ways of analyzing product design in order to identify how design changes will improve assembly and manufacturing efficiency. It focuses on manufacturing and assembly cost reduction using the process of Design for Manufacture and Assembly and it also addresses the product quality benefits that arise from the application of the Design for Manufacture and Assembly process.
The writer emphasizes how can basic three steps i.e., design for assembly selection of materials and processes, and design for individual part manufacture can produce dramatic cost reductions, coupled with substantial quality improvement.
The traditional practice of design for manufacture
The traditional practice of Design for Manufacture is part focused method. The term design for manufacture is applied to the process using rules or guidelines to assist in the design of individual parts for efficient processes. In Design for Manufacture, designers are provided with no. of rules for large no. of processes provided by the experts of each process. These rules can create vulnerability in other ways if these rules are made without regard to manufacturability capabilities and limitations. However, if Design for Manufacture rules are used as the main principles to guide a new design in the direction of manufacturing efficiency, then the result will usually be very unsatisfactory.
The new approach of design for manufacture and assembly
Rather than part focused new approach concentrates on the structure of the product and tries to reach the agreement on design agreement for minimization of manufacturing cost, assembly cost, and other cost. Design for manufacture and assembly used design for assembly as the primary method for decision-making for the purpose of making the structure of the product. The iteration process is followed until the optimal solution is found Design for assembly is the starting point for iteration and the iteration process stops when a robust system is obtained.
The part count is important for these processes, so simplification of parts is another important step with cost-effectiveness, quality, and durability in mind. Secondly, the identification of materials and processes is closely related to Design for assembly. Another part of Design for assembly is to control the manufacturing cost. Below is the chart that represents the process for Design Manufacturing and Assembly.
However, the cost of proposed new parts cannot be obtained until designs are available. The final stage of Design for manufacture and assembly is component design for efficient processing. It should occur only after the important decisions regarding the structure of the product and its process choices have been explored properly.
Design For Assembly
The role of DFA in product simplification
Design For Assembly (DFA) is a systematic analysis procedure used during the early stages of product design for assessing assembly difficulties and for estimating their cost and time. In case of difficulties, certain adjustment is made in design or assembly, and immediate feedback on the effect of change. Design For Assembly is also a medium for querying the relationship between the parts in a design and for attempting to simplify the structure through a combination of parts and features. The important role of Design For Assembly is to determine the most efficient faster methods in design. This is the most important aspect as it can be more labor-intensive in terms of mechanical assembly.
For example, for pressure recorder assembly around 47% of the assembly time is spent on the insertion and tightening of separate screws and nuts. To reduce the assembly cost of dealing with separate fasteners, fastening methods must be considered as an integral part of functional items. For plastic molded parts, well-designed snap fits of various types can often provide reliable and high-quality fastening arrangements that are extremely efficient for product assembly. Sheet metal parts might be made from spring steel to incorporate integral fastening features to save the cost of assembly. Metal parts may be made with projections for riveting or forming permanent joints or they can be press fitted together or contain threads for screw fastening.
Screw fastening is the most widely use process in almost all mechanical assembly, so special attention is worth paying but, in some ways, it is an inefficient method. The below table gives the industry average Design For Assembly time estimates for assembling a cover part to a base using a variety of alternative fastening arrangements.

The time required for press-fitting assumes the use of a small bench press with a foot pedal or similar control. The need for jar type cover, careful starting of the cover thread, and around five turns for full tightening are essential for fastening for screws. For rivet, the estimated time includes the use of a hand-loaded screw into the power tool. For the installation of separate screws, screw thread engagement is assumed to be done by hand followed by a power tool for tightening.
Screw fastening, despite being the inefficient method it is also one of the least reliable methods. They can be cross-threaded, or improperly torqued because of improper threads. Experiments conducted by Loctite Corporation show that transverse vibrations across a screw-fastened interface can rapidly unwind correctly torqued screws, even with any of the different types of standard lock washers.
Only trying to remove certain parts for time reduction doesn’t ensure optimal part count for example avoiding separate connectors and separate fasteners. In order to consider every possibility for reduction of no. of separate manufactured part in assembly, the BDI (Boothroyd Dewhurst, Inc.) Design For Assembly method is used. BDA works as a catalyst for brainstorming ideas for eliminating unnecessary parts.
A part is allowed to be defined as separate with respect to parts already assembled if (i) made from different material for some fundamental performance; (ii) moves in a rigid body fashion involving rotational or translational; (iii) separate for assembly. If three criteria, then they can be eliminated. In this way, Design For Assembly can simplify the design to reduce the cost and time.
The Design For Assembly time-standard system
The Design for Assembly method utilizes the database of standard times for handling and insertion which is based on part size, symmetry, and the method they are going to be used. Avoidance of those who suffer a significant time penalty on the assembly process represents the importance of good detail of the Design for Assembly. For this, there are two categories of part handling and part insertion.
Part Handling
Designing a part so they do not tangle, avoiding properly unshaped flexible parts, avoiding sharp edges where parts need to be handled manually, etc. are some rules in part handling.
Part insertion
Designing the parts to align easily, limiting forces during insertion of parts for manual assembly, choosing proper clearances, selecting the direction for assembly, ensuring adequate access for the parts, etc. are some sets of rules that need to be followed during part insertion.
Assembly problems are analyzed during DFA analysis. The result of the analysis is presented on a DFA worksheet.
Design For Assembly Index
The minimum no. of part counts that can be used to determine a Design For Assembly index includes the assessment of possible part-count redundancy and analysis of assembly difficulties in the design. This is defined as
- Design For Assembly Index = (Nm where Nm × tm)/ta×100
- Where Nm = theoretical minimum number of parts,
- tm = minimum assembly time per part,
- ta = estimated total assembly time.
For an ideal design for assembly which has minimum no. of items and no assembly, the Design For Assembly Index is 100. If for example, the Design For Assembly index score is 7, there is a need for significant assembly improvements.
Design For Assembly Case Study
The positive benefits of Design For Assembly product redesign can be seen in the case study from Texas Instruments. The original design of the gunsight mechanism is shown below. In this case study the original design was in production but due to advantageous redesign, the manufacturer used the new design. The part count reduction is more dramatic.
Operation Table Data
Table 1: Design For Assembly worksheet for the redesigned pressure recorder
Item name | Number of items/operations | Operation time, sec. | Minimum part count |
Pressure regulator | 1 | 3.5 | 1 |
Plastic cover | 1 | 7.4 | 1 |
Nut | 1 | 9.1 | 0 |
Knob | 1 | 8.4 | 1 |
Set screw tighten | 1 | 5.0 | — |
Reorient | 1 | 9.0 | — |
Apply tape | 1 | 12.0 | — |
Adapter nut | 1 | 12.0 | 0 |
Sensor | 1 | 9.9 | 1 |
PCB assembly | 1 | 7.6 | 1 |
Totals: | 10 | 83.9 | 5 |
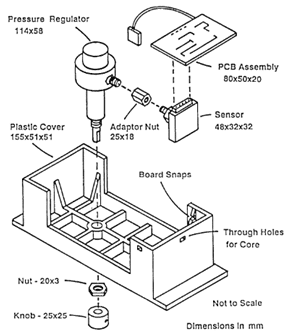
The effect of applying the minimum parts criteria during the analysis of the existing design can be considered for the case of compression springs. When the first spring is to be inserted in the carriage subassembly, it satisfies the need for a different material than exists in items already assembled. However, the other eight springs are made from the same material that is already present in the first springs, do not have to move in a rigid-body fashion, and do not have to be separate for assembly purposes. This may lead the designer to think about a single custom spring. It can be seen in the later figure.
Also, the below table shows the benefits of the redesigned gunsight mechanism. The reduction of assembly time is by 84.7 percent. Similarly, much larger achievement is gained in part manufacturing i.e., saving about 8.98 hours reduction compared to 1.82 hours saved in assembly time. This result is due to designing with greatly simplified structures resulting from the Design For Assembly application. Likewise, the elimination of parts also removes associated costs for purchasing, inventory, quality control, documentation, production control, and scheduling.
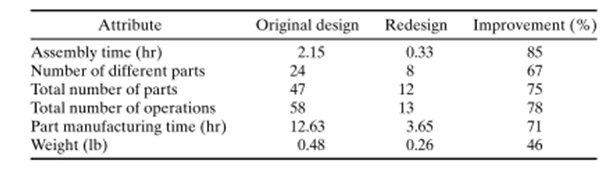
Assembly quality
Design for assembly has been used by Motorola Inc. since the mid-1980s for simplification of products and reduction of costs. Due to Design for Assembly, the benchmarking of competitors’ electronics products indicated a best-in-class Design For Assembly Index value of 50 percent, and they designed many concepts to redesign that goal. The final design has 78 percent fewer parts than their previous vehicle adapter and an 87 percent reduction in assembly. There is also a significant reduction in defect rates.
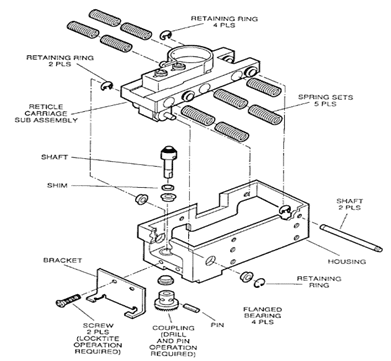
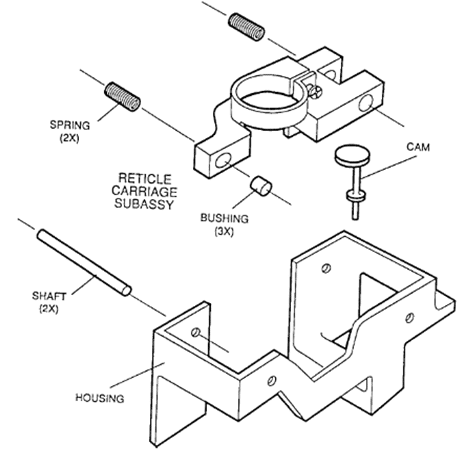
Motorola engineers surveyed a no. of products which have been analyzed using Design For Assembly and produced a correlation between assembly defects per part and the DFA Index. This clearly shows a clear relationship between assembly quality and Design For Assembly Index values. Other researchers postulated that since assembly time can be related to the increasing difficulty of assembly operations, then the probability of an assembly error may also be a function of assembly operation time.
In the study, it was reported that 50 combinations of defect rates to assembly characteristics were tested for meaningful correlation. Of these, the variation of average assembly defect rate per operation with average Design For Assembly time estimate per operation showed the strongest linear correlation, with correlation coefficient r = 0.94. The equation of the regression line is given by
- Di = 0.0001 (ti − 3.3)
- Where Di = average probability of assembly defect per operation
- ti = average assembly time per operation
- The average assembly time for small parts that present no assembly is around 3 seconds from the DFA time-standard database. So, the above for a product requiring n assembly operations, the probability of one or more assembly defects is
- Da = 1 − [1 − 0.0001 (ti − 3.3)]n
This relationship can be easily applied in the early stages of design to compare the possible assembly reject rates. This can provide direction to product quality improvement.
For the pressure recorder, the existing design has an average Design For Assembly assembly time per operation of 8.95 seconds for a total of thirty-four operations. The above equation gives an estimated probability of a defective assembly as 13 per 1000s.
Table 2
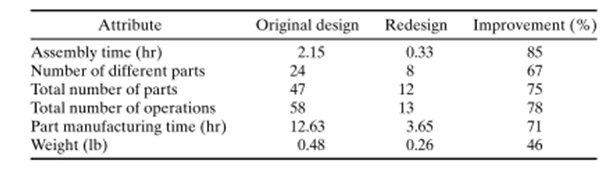
shows the DFA Results from 94 Published Case Studies.
Category | No. of cases | Average reduction (%) |
Part count | 80 | 53 |
Assembly time | 49 | 61 |
Product cost | 21 | 50 |
Assembly cost | 17 | 45 |
Assembly operations | 20 | 53 |
Separate fasteners | 15 | 67 |
Labor costs | 8 | 42 |
Manufacturing cycle | 6 | 58 |
Weight | 6 | 31 |
Assembly tools | 5 | 69 |
Part cost | 4 | 45 |
Unique parts | 4 | 59 |
Material cost | 4 | 32 |
Manufacturing process steps | 3 | 45 |
No. of suppliers | 4 | 51 |
Assembly defects | 3 | 68 |
Cost savings per year | 6 | $1,283,000 |
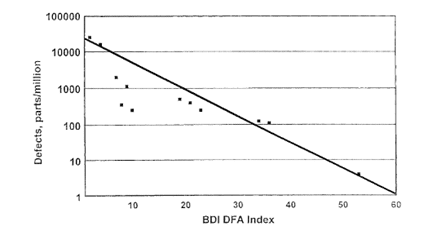
Choice of Materials and processes
Designers consider only a few ranges of material and process combinations for product design. This can lead to too-short design time and process in which they are comfortable and familiar. So, the art of possible and low-cost manufacturing costs is overlooked. In the 1980s, a FORTRAN-based program called MAPS was developed to choose the material and process selection. With the help of this program, primary shapes, part size, and geometry classification were able to achieve. However it didn’t allow for the stock form availability, and it didn’t allow for the possibility of a sequence of programs to satisfy the desired requirements.
To overcome this a commercial relational database system called CAMPS (Computer-aided material and process selection) was built. However, experience with it has led to both material performance and geometric shape requirements for such a system being too constraining. Later, Ashby and Dieter developed the relation which defines the property for bending stiffness per weight and is given by
- P1 = E1/3 /ρ
- Where E = Young’s modulus
- Ρ = material density
Material that has a high value of P1 can be investigated with regard to shape possibilities and comparative cost. Irrespective of material selection, cost is also very important. So, early cost estimation during the design process is very important.
Detail Design for Manufacture
The details of each part have a substantial effect on the cost of individual items. A study of Rolls Royce in the UK finds out that 30 percent of the avoidable costs would have resulted from changes in the detail design of parts. Thus, Design for Manufacture checks on part design should not be forgotten. For the pressure recorder, the snap-fit features in the cover were justified for the resulting savings in assembly cost. However, the proposed design may possibly be improved which can save more money in the molding process of this snap fit.
Concluding Comments
Assembly is also a vital part of manufacturing products. Effective Design for Manufacture must address this despite assembly being the final step of manufacture. As a result, the product will be driven toward simplicity of product and wide-ranging benefits in every activity from material or parts procurement to reliability and customer satisfaction.